Product
Are You Looking For Hexagon Socket Screws?
Fixicore is an hexagon Socket Screw manufacturer for screw,bolt and nut. Our fastener factory in China adhere to ANSI, DIN, BS, JIS, China GB standards and customer specific requirements. Our products have been sold worldwide for a wide range of applications in auto, oil refining, chemical, marine, power generation and pipeline transportation and other industries.
REQUEST A QUOTE FOR MORE DETAILS
The Ultimate Guide Of Socket Screws
Screw Sizes, Types, Uses and More
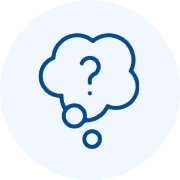
What Are Socket Screws?
Chapter 1
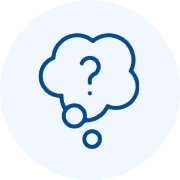
Types of the Socket Screw and Functions
Chapter 2
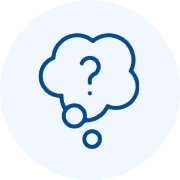
Socket Set Screw Point Styles
Chapter 3
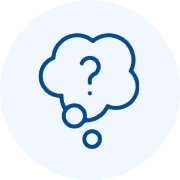
Socket Screw Materials?
Chapter 4
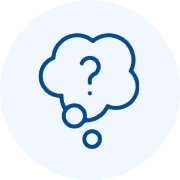
Socket Screw Finishes
Chapter 5
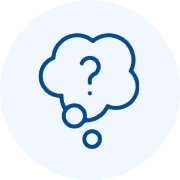
What Are Socket Screws?
Chapter 6
Chapter 1
Request A Free Quote
We'd like to work with you
Send us a message if you have any questions or request a quote. Our experts will give you a reply within 24 hours and help you select the right valve you want.
- +86 577 5768 9696
- sales@fixicore.com
What Are Socket Screws?
In the world of fasteners, socket screws, also known as socket head cap screws (SHCS), are among the most commonly utilized elements. They are specifically designed to fasten two components with high precision and security.
A socket screw is characterized by a cylindrical head with a hexagonal drive hole, intended to accommodate an Allen wrench or hex key. The design of the socket screw allows for a higher torque to be exerted compared to a conventional screw with a similar diameter, making it an excellent choice for applications where high clamping force is required.
Manufactured from various materials such as stainless steel, alloy steel, and even brass, socket screws come in an array of sizes and lengths. The application or purpose of use typically determines the choice of material and size. Stainless steel socket screws, for example, are widely used for their corrosion resistance, making them ideal for outdoor applications or in environments where they may be exposed to moisture.
The brilliance of the socket screw design lies in its minimalistic head, which allows it to be used in situations where a low-profile fastener is needed, or space is limited. Furthermore, the socket head makes it easier to insert and remove the screw in areas where access is difficult.
In conclusion, socket screws are a crucial player in the fastening world due to their versatility, strength, and ease of use. They are used in a wide range of industries, including automotive, aerospace, and manufacturing, reflecting their importance in creating robust and reliable connections. Regardless of your project’s complexity, there’s likely a socket screw that fits the bill, offering the combination of strength and precision that you need.
Chapter 2
Types Socket Screws And Their Functions
In the vast world of fasteners, the socket screw family holds a significant position due to its wide range of types, each serving specific purposes. Here, we’ll explore the various types of socket screws and their functions, including set screws.
- Socket Head Cap Screws (SHCS): These are arguably the most common type of socket screws. As their name implies, they feature a cylindrical cap head and a hexagonal drive hole. SHCS are perfect for applications demanding high precision and strength due to their capability to withstand high torque. They’re widely used in machine parts, die fixturing, and clamping.
- Button Head Socket Screws: This variant features a rounded head that is lower and wider than that of the SHCS. The button head provides a neat finish, making it a preferred choice for decorative purposes or applications where the screw must not protrude above the surface.
- Flat Head Socket Screws (Countersunk): These screws have a conical head that, when installed, aligns flush or below the surface of the assembly. Flat head socket screws are ideal for applications where a smooth surface finish is required to avoid interference or snagging.
- Low Head Socket Screws: Designed with a lower profile head than the SHCS, these screws are suitable for jobs with limited overhead space. Despite their low profile, they still maintain a high degree of tensile strength.
- Socket Shoulder Screws: These are unique in the sense that they have a cylindrical, larger diameter shoulder under the head. They serve as a shaft or dowel for rotating items like gears and pulleys, with the shoulder providing a precise guiding surface.
- Socket Set Screws: Set screws are fundamentally different from the other types mentioned above. They lack a head and are fully threaded. These screws are used to secure an object within or against another object. The most common use is to secure a pulley or gear to a shaft. They exert a compressional force through the tip that projects onto the object.
- The tip of a set screw can have several designs – cone point (for permanent installations), cup point (for a semi-permanent solution), and flat point (used when minimal surface damage is desired), among others.
To conclude, socket screws, given their various types, offer a high level of versatility in different applications. From the automotive industry to home DIY projects, their unique designs meet the needs of a multitude of fastening tasks. Understanding the distinctive features and uses of each type will help you make an informed decision for your specific needs, ensuring secure, robust, and efficient connections.
Chapter 3
Socket Set Screw Point Styles
Socket set screws are unique, headless fasteners typically used to secure an object within or against another object. Their design differs significantly from standard screws, with the key distinctive feature being the point styles at the screw’s end. Each point style serves a different purpose and offers varying levels of hold. In this article, we will delve into the various socket set screw point styles, explaining their distinctive features and applications.
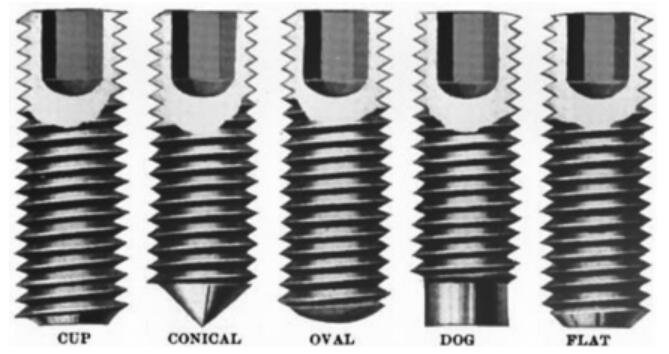
- Cup Point: The most common type of set screw, the cup point, has a cup-shaped indentation at the tip, designed to dig into the contact material and provide a strong, secure hold. This type is highly versatile and ideal for semi-permanent to permanent applications where re-adjustment is not typically required. Industries such as manufacturing and construction frequently use cup point set screws.
- Cone Point: These screws have a sharp, conical point that embeds itself within the part it is securing, resulting in the highest tightening torques among all set screw types. This makes cone point set screws suitable for permanent installations where the secured parts must not move at all. They are also commonly used in thin-walled parts or in applications where a pivot point is needed.
- Flat Point: Flat point set screws are characterized by a flat surface at the tip, exerting a broad contact on the object. This type causes the least damage to the shaft of all the point styles, which makes them ideal for applications where damage to the contact surface should be minimized. Flat point set screws are commonly used in situations where frequent repositioning is needed.
- Dog Point: A dog point set screw has an extended, flat tip that protrudes from the threaded part of the screw. This extended point serves as a shaft, allowing the screw to align parts or to act as a pivot or hinge. They are frequently used in applications such as gear assemblies, where alignment is crucial.
- Knurled Cup Point: This is a variation of the cup point, but with a knurled surface. The knurling allows for a tighter grip, particularly useful in applications involving vibration, such as in engines or heavy machinery. The knurled cup point set screws offer superior resistance against loosening.
- Oval Point: The oval point set screw has a rounded, oval-shaped point that allows for frequent re-adjustments without damaging the contact material. This point style combines the advantages of both the cup and cone point set screws, offering a strong hold while minimizing material damage. They are ideal for applications that require regular fine-tuning.
- Half-Dog Point: Similar to the dog point, half-dog points have a protruding tip, but it’s only half the diameter of the screw. They are often used in applications where minimal protrusion is required.
In conclusion, the various point styles of socket set screws each serve distinct purposes, allowing for the customization of fastening solutions based on the specific requirements of an application. By understanding the strengths and uses of each point style, one can make an informed decision, ensuring secure, robust, and efficient fastening, whether it’s in industrial applications or everyday household tasks. It’s a testament to the sophistication of the humble screw, demonstrating its essential role in keeping our mechanical world securely fastened.
Chapter 4
Socket Screw Material: A Comprehensive Guide
Socket screws, with their unique design and versatility, play a vital role in various applications, from electronics and home appliances to aerospace and construction. An important characteristic that affects the screw’s performance, durability, and applicability is the material it’s made of. In this article, we’ll examine the different materials commonly used to manufacture socket screws.
- Stainless Steel: One of the most prevalent materials for socket screws is stainless steel, known for its corrosion resistance and durability. Stainless steel socket screws are commonly used in environments where they may be exposed to moisture, chemicals, or high temperatures. Two common types of stainless steel used are 304 and 316, with the latter offering greater corrosion resistance, particularly in saltwater environments.
- Alloy Steel: Socket screws are often made from alloy steel, which is a steel that has been mixed with other elements to improve its properties. Alloy steel screws have a high tensile strength and are usually heat-treated for additional hardness, making them ideal for heavy-duty applications that demand durability and strength. They are typically coated or plated to provide corrosion resistance.
- Brass: Brass, an alloy of copper and zinc, is often used in the manufacturing of socket screws due to its good corrosion resistance and electrical conductivity. Brass socket screws are primarily used in applications where low magnetism is necessary or in decorative functions due to their gold-like appearance.
- Titanium: While not as commonly used due to its high cost, titanium offers excellent strength-to-weight ratio and outstanding corrosion resistance. Titanium socket screws are used in high-performance applications like in the aerospace and marine industries.
- Aluminum: Aluminum screws are lightweight and resistant to corrosion, but not as strong as steel. They’re suitable for light-duty applications where weight is a concern, such as in consumer electronics.
- Plastic: Certain applications, especially those that require electrical or thermal insulation, might utilize plastic socket screws. These screws are also resistant to corrosion but are generally not as strong or durable as their metal counterparts.
In conclusion, the choice of material for a socket screw significantly influences its performance and application suitability. It’s crucial to consider factors such as the operating environment, load requirements, and desired durability when selecting the appropriate material for your specific application. By understanding the different materials available, you can make the best choice for your fastening needs.
Chapter 5
Socket Screw Finishes
A socket screw’s finish is more than just about its aesthetics; it can significantly influence the screw’s performance, corrosion resistance, and longevity. There are several types of finishes that can be applied to socket screws, each with its unique benefits and suited applications. This article will guide you through the various socket screw finishes and their purposes.
- Plain (Unfinished): Socket screws may sometimes be left unfinished, often when corrosion resistance isn’t required, such as in indoor, dry, or low-stress environments. The material of the screw, like stainless steel, may naturally provide sufficient corrosion resistance.
- Zinc Plating: One of the most common finishes, zinc plating provides good corrosion resistance at a low cost. Zinc-plated socket screws are typically used in outdoor applications. For enhanced protection, a chromate conversion coating can be applied over the zinc plating.
- Black Oxide: This finish provides a dark black appearance and minor corrosion resistance. Black oxide finishes are commonly used on socket screws for aesthetic purposes, especially when a dark color is desirable to blend with the assembly.
- Nickel Plating: Nickel-plated socket screws offer excellent corrosion resistance and a bright, decorative finish. They are often used in environments where they’ll be exposed to high temperatures or corrosive elements.
- Hot Dip Galvanizing: This process involves coating the screw in a layer of zinc by dipping it in a molten zinc bath. Hot dip galvanized screws have excellent corrosion resistance, making them suitable for marine and industrial applications.
- Cadmium Plating: Cadmium plating provides superior corrosion resistance and excellent lubricity, meaning screws with this finish are less likely to seize. However, due to environmental and health concerns, its use is less common now.
In conclusion, the type of finish on a socket screw can greatly impact its functionality and lifespan, as well as its aesthetics. When selecting a finish for your socket screws, it’s essential to consider the environment in which the screw will be used, the desired appearance, and the level of corrosion resistance needed. By understanding the various finishes available, you can ensure that your fastening solution is both durable and visually appealing.
Chapter 6
Socket Screw Features
Socket screws are indispensable components in a myriad of applications due to their specific design and distinctive features. These features equip the screws with the ability to provide secure, robust, and precise fastening solutions. In this article, we delve into the unique characteristics that define socket screws.
- Hexagonal Socket Drive: A key feature of socket screws is the hexagonal socket drive. This design allows for a higher torque to be exerted than a conventional screw of the same diameter, facilitating a strong, secure fastening.
- Cylindrical Head Designs: Socket screws are typically characterized by a cylindrical head, which can come in various styles such as button, flat, and low profile, each offering unique benefits. This head design allows for use in tight spaces or where a low-profile fastener is needed.
- High Material Strength: Socket screws are often made from high-strength materials such as stainless steel or alloy steel, providing excellent durability, corrosion resistance, and ability to withstand high pressures and temperatures.
- Full or Partial Thread: Socket screws can have either full or partial threading, depending on the requirements of the application. Full-threaded screws offer superior grip in softer materials, while partially threaded screws allow for a smooth, unthreaded portion under the head, beneficial in applications requiring alignment.
- Various Sizes and Lengths: Socket screws are available in an array of sizes and lengths to suit a wide range of applications. From minute screws used in electronic devices to large, heavy-duty screws for construction, the selection caters to all needs.
- Secure Fastening: The design of socket screws allows them to be securely fastened into place, reducing the risk of loosening over time due to vibration or stress. This is particularly useful in applications such as machinery, where safety and reliability are paramount.
In conclusion, socket screws, with their distinct features, offer a reliable, versatile, and efficient fastening solution in various applications across numerous industries. Their high strength, ease of use, and compatibility with high-torque operations underline their importance in ensuring secure and durable connections. By understanding these features, users can ensure they choose the most effective socket screw for their specific fastening needs.
In Summary
The wide screw of Fastener can overwhelm the buyer. However, if equipped with the right industrial information, decision making becomes much easier. screws vary in their functions. By knowing the purpose of the screw narrows the list of fastener choices. This article has discussed what one needs to know before buying Socket screws.
Request A Free Quote
We'd like to work with you
Send us a message if you have any questions or request a quote. Our experts will give you a reply within 24 hours and help you select the right valve you want.
- +86 577 5768 9696
- sales@fixicore.com